brewzone
Regular.
Below are graphs showing the effect of Kp Ki and Kd on an Arduino Mega Output running the PID Libraries using PWM.
I expect there will be no noticeable change using Time Proportional.
Figure 0 shows Kp=255 Ki=0 and Kd=0
Figure 8 shows what I found to be the perfect settings for 18L in a 33L Nordic Stockpot using a 2.4kwh Backer heating element.
This is intended for use as an HLT.
If used in a Herms or Rims I imagine the values will be very different.
Figure 0 and Figure 8 give the fastest ramp time and fastest to settle to steady state of 2.35%
I expect there will be no noticeable change using Time Proportional.
Figure 0 shows Kp=255 Ki=0 and Kd=0
Figure 8 shows what I found to be the perfect settings for 18L in a 33L Nordic Stockpot using a 2.4kwh Backer heating element.
This is intended for use as an HLT.
If used in a Herms or Rims I imagine the values will be very different.
Figure 0 and Figure 8 give the fastest ramp time and fastest to settle to steady state of 2.35%
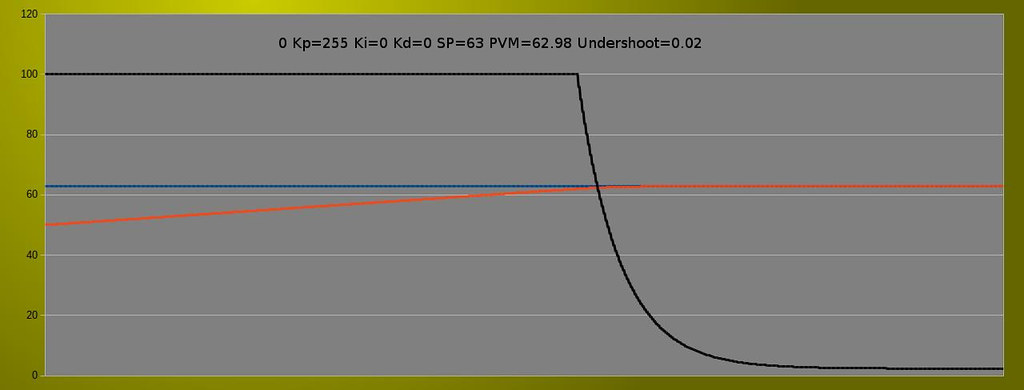
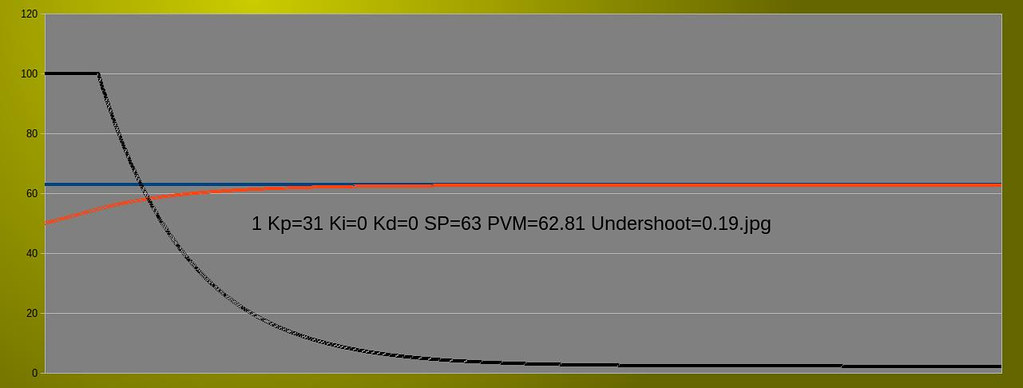
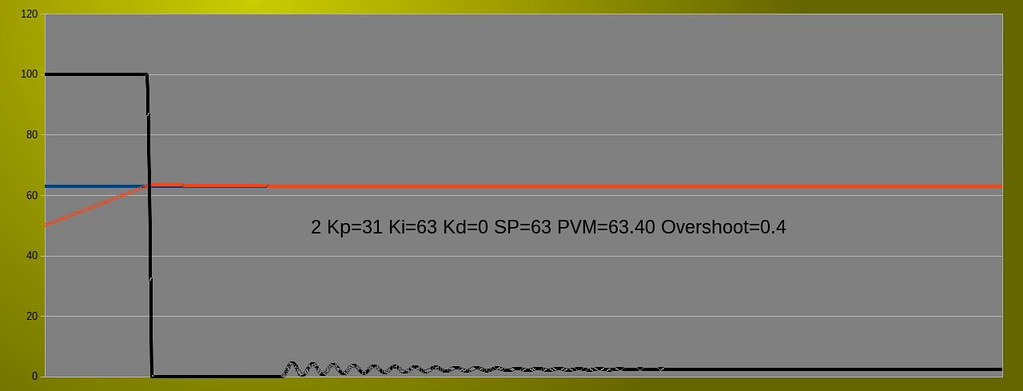
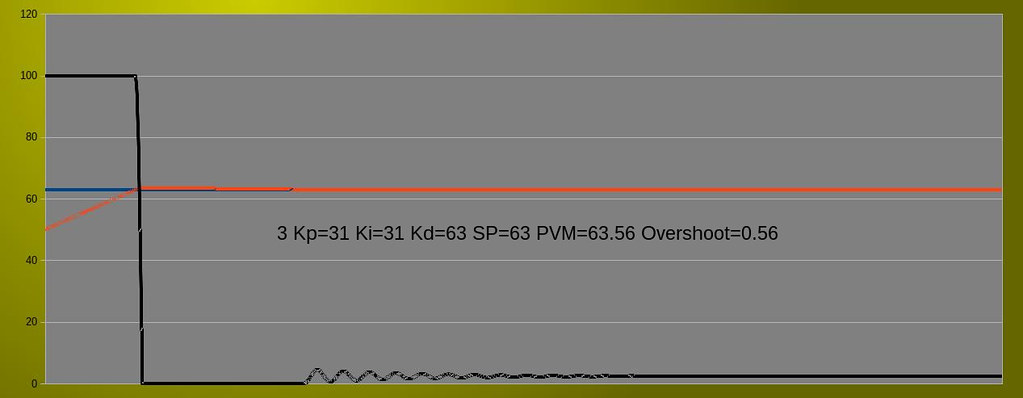
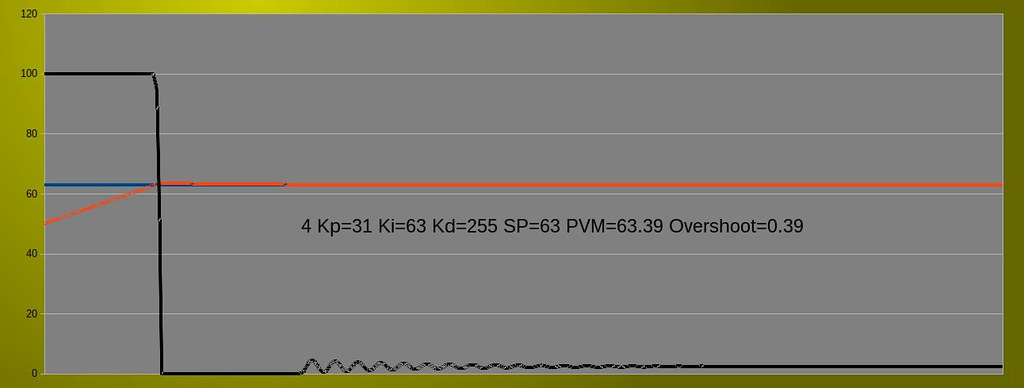
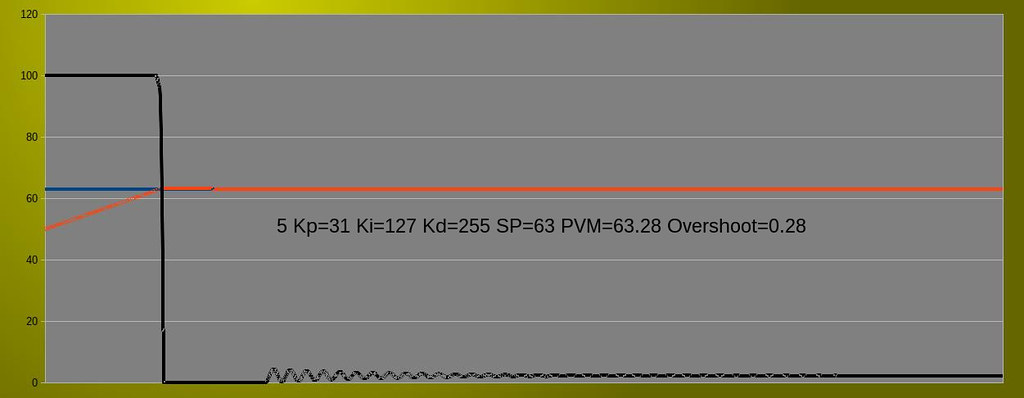
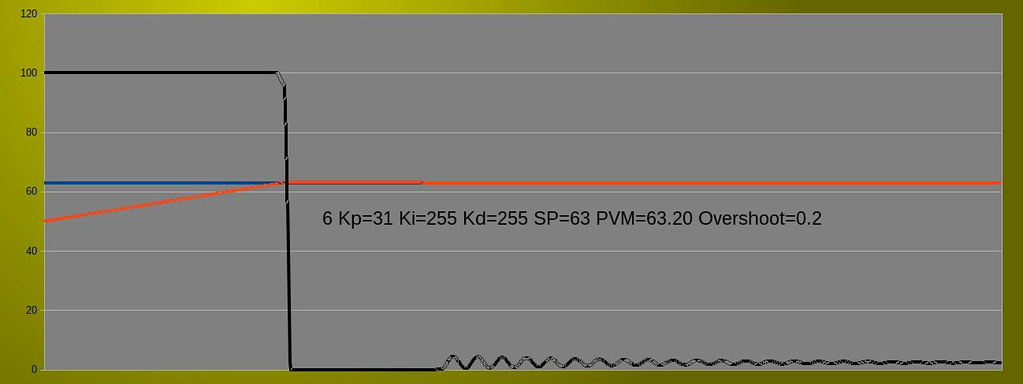
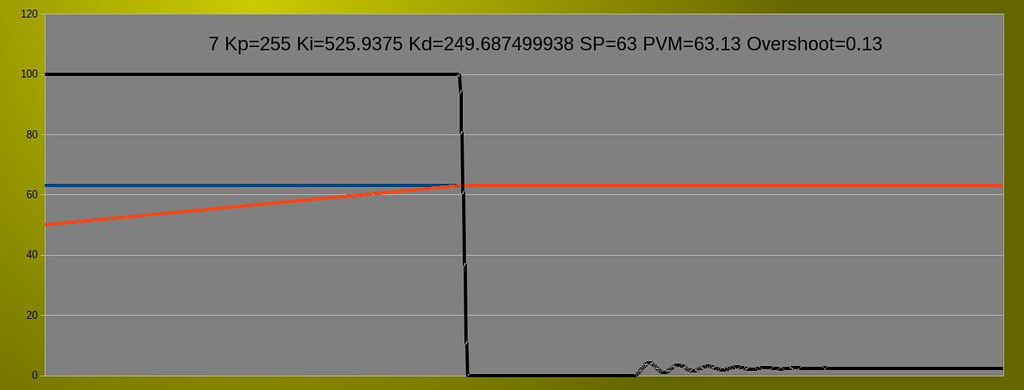
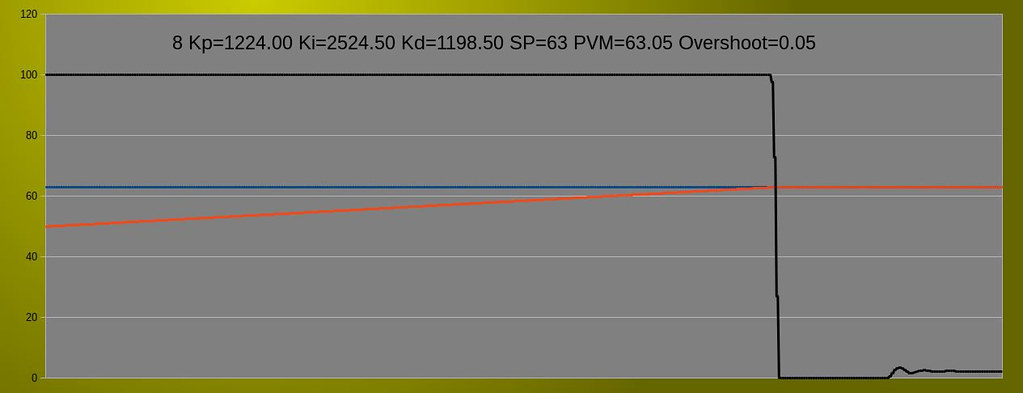