beer taster
Well-Known Member
Hi All
I'm currently in the process of tinkering with the brewery. Just added a Valentines Arm, now planning an automatic underback so I can fly sparge using the V-Arm and pump the wort from an underback to the boiler.
I plan to use a Stainless pot (not sure what size probably 5-10L) as the underback and put 2 float switches in the pot. When the wort reaches the uppermost switch it turns on the pump and pumps the wort to the boiler, when the level drops below the lower switch it turns off the pump.
The float switches I will be using can be found HERE
Below is my planned wiring of the float switches. When the wort level in the underback hits FS1 nothing happens. When it hit FS2 the pump is turned on and will stay on until the level drops below FS1 the pump will turn off.
Will this work. :hmm:
I'm currently in the process of tinkering with the brewery. Just added a Valentines Arm, now planning an automatic underback so I can fly sparge using the V-Arm and pump the wort from an underback to the boiler.
I plan to use a Stainless pot (not sure what size probably 5-10L) as the underback and put 2 float switches in the pot. When the wort reaches the uppermost switch it turns on the pump and pumps the wort to the boiler, when the level drops below the lower switch it turns off the pump.
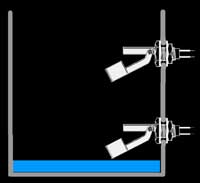
The float switches I will be using can be found HERE
Below is my planned wiring of the float switches. When the wort level in the underback hits FS1 nothing happens. When it hit FS2 the pump is turned on and will stay on until the level drops below FS1 the pump will turn off.
Will this work. :hmm:
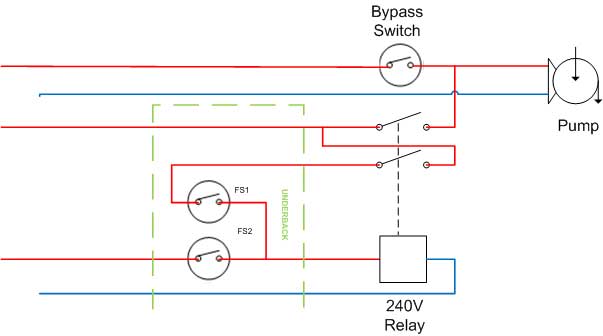