AndyBWood
Regular.
Evening All,
First off, thanks for everyoneâs input on this; as always, much appreciated. :thumb:
Finally put this together at the weekend; it took a while but, to honest, once I had all the bits& bobs in front of me it was pretty straightforward.
By far the hardest task was cutting the reception holes for the PID, sensor and power leads but Dremell and Stanley Knife came into their own. I had a few âwonderingsâ with said items and a couple of scars remain ( the box not me ! ) but thatâs being hyper critical. Overall, it went well.
I used a 3 pin DIN plug to connect the sensor which was a bit of a pain. Unfortunately, Iâd already ordered this before reading the XLR suggestions which, as a bulkier component, would probably have been far easier.
Round the back I used a combined in / out socket which keeps things as tidy as possible.
Inside, its pretty straightforward. Again taking onboard the consensus, I shelved the plans to install some type of fan. Having run the PID solid for a good hour the heatsink seems to cope well enough. I did, however, drill a good handful of extra holes in the base of the box to encourage more airflow.
Seems to work fine. I also used a good smear of heatsink compound where the SSR seats; the kind of paste used on computer CPUs.
One thing lacking at the moment is a 3 amp fuse in line with the PID itself which Iâll attend to this week.
After letting the PID autotune with around 35 litres of water at 85 degrees it seems to hold the temp around +/- 0.2 degrees of target which, for my sparging purposes is, I hope, accurate enough. I might have a tinker with the parameters to see if I can get closer; just for fun mindâ¦..
So the weekend beckons, AG2 and, maybe, Worthington White Shield. Iâm sure building the PID wonât help me make better beer but HLT temp is now just one less thing to worry about plus a real sense of satisfaction having put something like this together.
Thanks again for all the help. :thumb:
Andy
First off, thanks for everyoneâs input on this; as always, much appreciated. :thumb:
Finally put this together at the weekend; it took a while but, to honest, once I had all the bits& bobs in front of me it was pretty straightforward.
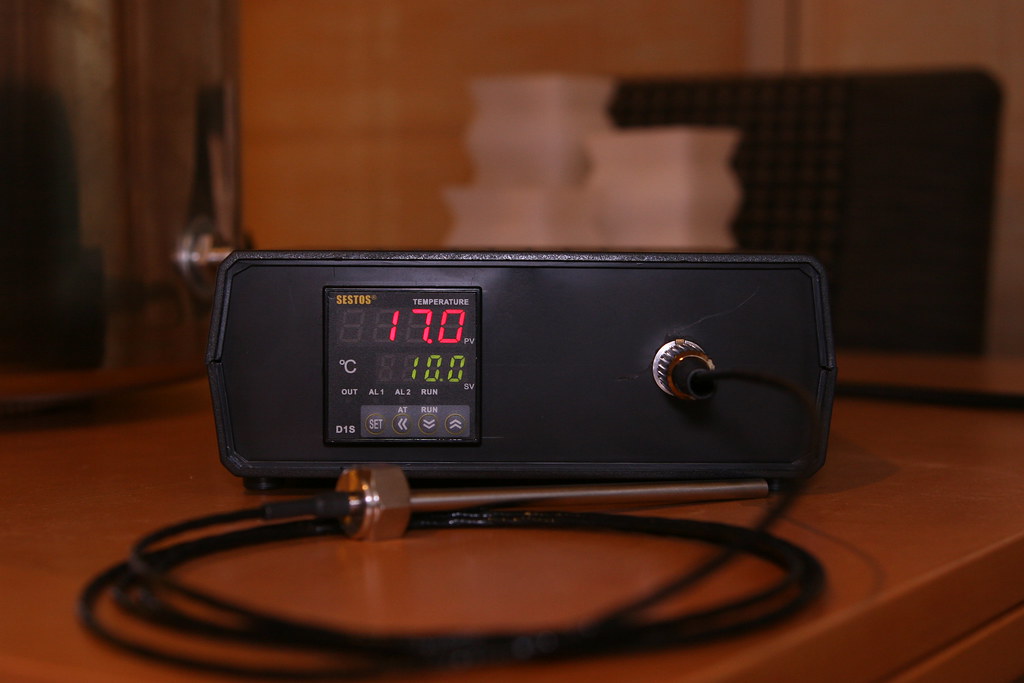
By far the hardest task was cutting the reception holes for the PID, sensor and power leads but Dremell and Stanley Knife came into their own. I had a few âwonderingsâ with said items and a couple of scars remain ( the box not me ! ) but thatâs being hyper critical. Overall, it went well.
I used a 3 pin DIN plug to connect the sensor which was a bit of a pain. Unfortunately, Iâd already ordered this before reading the XLR suggestions which, as a bulkier component, would probably have been far easier.
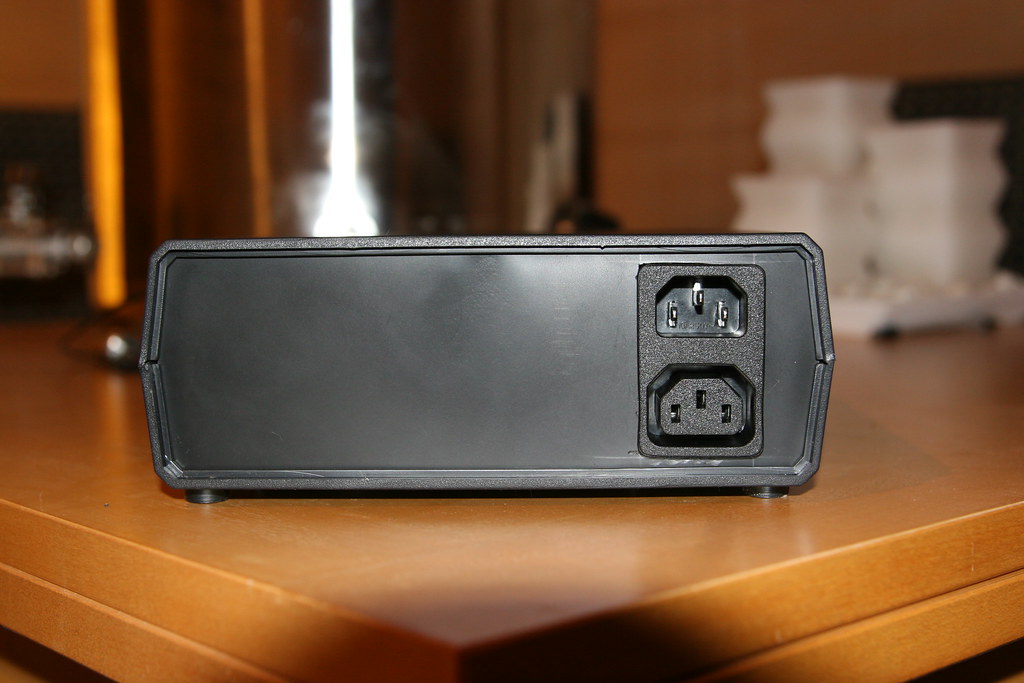
Round the back I used a combined in / out socket which keeps things as tidy as possible.
Inside, its pretty straightforward. Again taking onboard the consensus, I shelved the plans to install some type of fan. Having run the PID solid for a good hour the heatsink seems to cope well enough. I did, however, drill a good handful of extra holes in the base of the box to encourage more airflow.
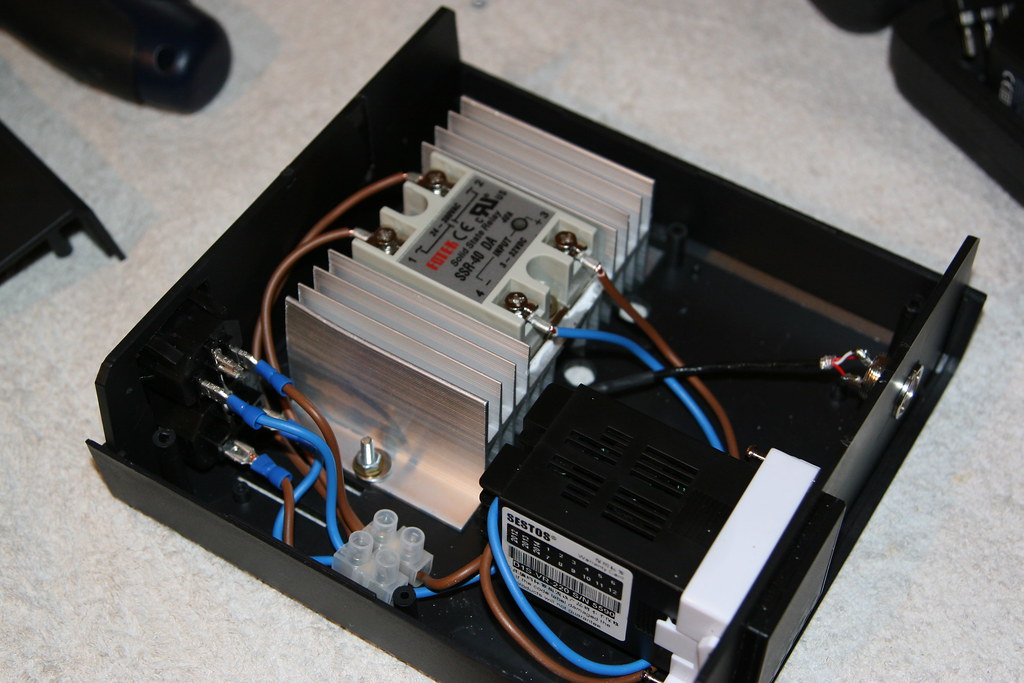
Seems to work fine. I also used a good smear of heatsink compound where the SSR seats; the kind of paste used on computer CPUs.
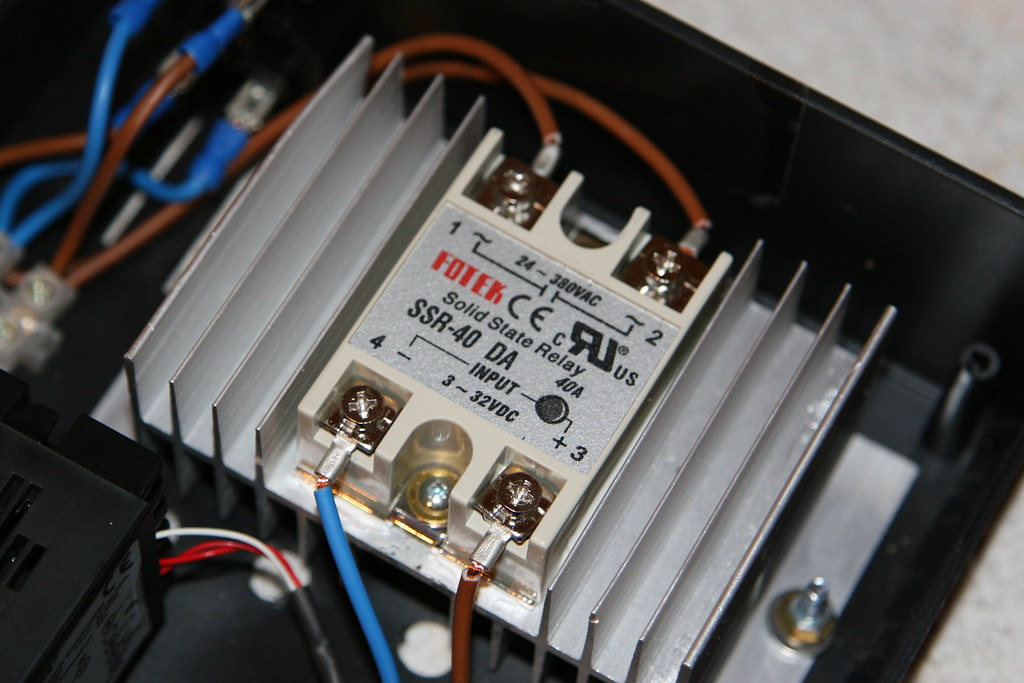
One thing lacking at the moment is a 3 amp fuse in line with the PID itself which Iâll attend to this week.
After letting the PID autotune with around 35 litres of water at 85 degrees it seems to hold the temp around +/- 0.2 degrees of target which, for my sparging purposes is, I hope, accurate enough. I might have a tinker with the parameters to see if I can get closer; just for fun mindâ¦..
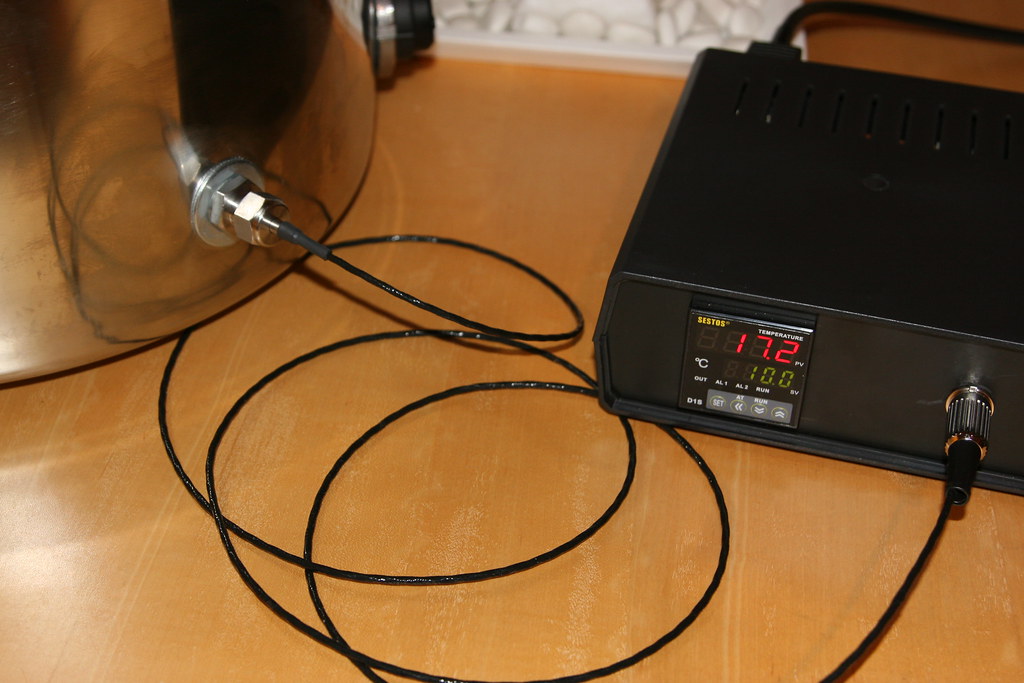
So the weekend beckons, AG2 and, maybe, Worthington White Shield. Iâm sure building the PID wonât help me make better beer but HLT temp is now just one less thing to worry about plus a real sense of satisfaction having put something like this together.
Thanks again for all the help. :thumb:
Andy